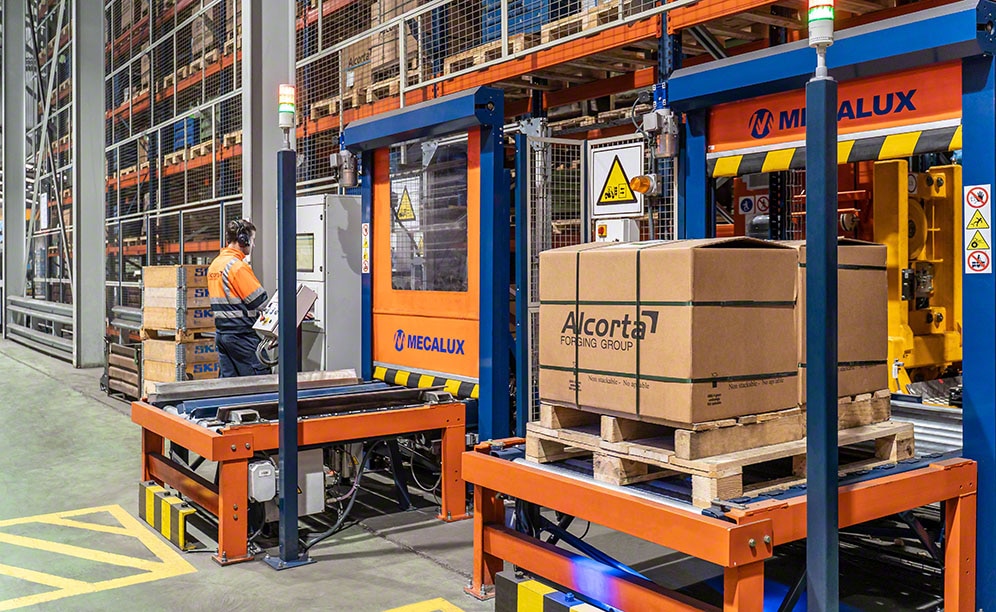
Alcorta Forging Group : la technologie reliant l'entrepôt à la production
Alcorta Forging Group a installé un entrepôt automatisé de pièces automobiles géré par Easy WMS

La transformation et l’amélioration continue font partie de l’ADN de la société métallurgique Alcorta Forging Group. Dans cet esprit, elle a installé un entrepôt automatisé de 14 mètres de haut ayant une capacité de stockage de 1 115 palettes dans son usine de production d’Elgóibar (Pays basque). Supervisé par le logiciel de gestion d’entrepôt Easy WMS de Mecalux, l’entrepôt déplace environ 300 palettes par jour (entrée comme sortie des matières premières et des produits finis) avec précision et sécurité.
Forger des solutions
Alcorta Forging Group est une entreprise centenaire dans le secteur de la métallurgie. Basée à Elgóibar (Pays basque), elle est présente en Allemagne, en France, en République Tchèque, en Afrique du Sud, en Chine et aux États-Unis. Ses origines remontent à 1911, date à laquelle elle a démarré la fabrication d’armes. Depuis les années 80, elle conçoit et développe des composants et pièces détachées pour les entreprises du secteur automobile. L’entreprise se caractérise par la qualité de ses produits, sa recherche constante en matière d’innovation et son engagement envers le respect de l’environnement.
Avec un chiffre d’affaires annuel de plus de 70 millions d’euros, dont 85 % à l’export (principalement vers la France, l’Allemagne et l’Afrique du Sud), Alcorta Forging Group s’est imposée comme l’une des entreprises espagnoles ayant le plus grand rayonnement.
Le moteur du centre de production
L’entreprise possède une usine de production à Elgóibar (Pays basque) où elle fabrique et distribue chaque année près de 20 millions de pièces et composants pour les marques leaders de l’automobile. Pour Alcorta Forging Group, la satisfaction du client est une priorité, c’est pourquoi son travail au quotidien consiste à concevoir et développer de nouvelles solutions répondant aux besoins d’un marché de plus en plus exigeant. José Antonio Fernández, responsable de l’entrepôt d’Elgóibar, souligne que l’entreprise transforme et améliore assidûment toutes ses opérations afin de les rendre plus efficaces : « Nous vivons actuellement un processus de croissance sans précédent. Pour servir un plus grand nombre de clients, nous nous efforçons d’améliorer et d’automatiser tous nos processus, y compris la logistique. ».
Conformément à cet objectif, Alcorta Forging Group a inauguré un entrepôt automatisé connecté de manière bidirectionnelle aux lignes de production. Il a pour fonction de stocker les matières premières qui doivent ensuite être envoyées à l’usine et, en même temps, de stocker et d’expédier les produits finis. José Antonio Fernández insiste sur le fait que, « avec ce projet, nous souhaitons réaliser un suivi fiable des stocks, de l’arrivée des matières premières à l’envoi des commandes aux clients ». En tenant compte de ces paramètres, le logiciel de gestion d’entrepôt Easy WMS de Mecalux a été installé. Ce logiciel centralise toutes les informations sur les produits et surveille leurs mouvements au sein de l’entrepôt, garantissant ainsi une entière traçabilité.
Concernant la conception du magasin, Fernández ajoute que « nous voulions exploiter la hauteur du bâtiment pour obtenir une plus grande capacité de stockage ». Le magasin mesure 13 m de haut et 54 m de long. Ses deux allées à rayonnage à simple profondeur lui permettent de stocker 1 115 palettes contenant plus de 300 références différentes.
Une solution automatique
L’entrepôt se compose de deux zones de travail clairement différenciées :
- Face avant des rayonnages (connexion à la production) : les produits finis sont reçus et les matières premières sont expédiées à l’usine.
- Côté de l’entrepôt (connexion avec les quais de chargement et déchargement) : c’est ici qu’arrivent les matières premières envoyées par les fournisseurs ou autres usines de l’entreprise et que les produits finis sont, à leur tour, expédiés aux clients finaux.
Chaque jour, 150 palettes en tout sont réceptionnées (en provenance des quais et de la production). Elles doivent toutes passer par un poste d’inspection où leur poids, leurs dimensions et leurs caractéristiques sont validés et reconnus conformes aux paramètres établis et requis dans l’entrepôt. À ce même poste, Easy WMS identifie chaque article et le saisit dans le système.
Ensuite, il lui attribue un emplacement en fonction de son niveau de demande et de sa typologie, à savoir s’il s’agit d’un produit fini ou d’une matière première. « Cette méthode de travail nous a permis d’optimiser les ressources dédiées au contrôle du stock », explique José Antonio Fernández. La bonne organisation de la marchandise dans l’entrepôt a un impact positif sur toutes les opérations. Selon le directeur de l’entrepôt, « nous sommes désormais en mesure de réaliser les tâches de stockage et de préparation des commandes de manière plus souple et rapide ».
De plus, Easy WMS connaît automatiquement l’emplacement exact de chaque article, à tout moment. La traçabilité complète de la marchandise réduit considérablement la possibilité de commettre des erreurs. Easy WMS est intégré à l’ERP d’Alcorta Forging Group. Les deux systèmes communiquent de manière permanente et bidirectionnelle dans le but de gérer l’entrepôt efficacement et de rentabiliser tous les processus logistiques.
Dans chaque allée, un transstockeur à deux colonnes déplace les palettes des positions d’entrée à l’emplacement attribué par le WMS, à une vitesse de translation de 120 m/min. Ces équipements automatiques rationalisent les processus dérivés du stockage, de la préparation et de l’expédition de la marchandise. Comme pour les entrées, 150 palettes quittent chaque jour l’entrepôt avec deux destinations possibles : d’une part, les matières premières envoyées en production et, d’autre part, les commandes distribuées aux clients. Les palettes quittent l’entrepôt de manière séquencée en tenant compte de la commande ou de l’itinéraire de transport. Elles restent groupées en attendant d’être chargées dans le camion de transport.
Les avantages d’installer un entrepôt automatisé
- Productivité et disponibilité. L’entrepôt peut fonctionner 24 heures sur 24 à plein régime.
- Une réduction des coûts d’exploitation. Comme il fonctionne de manière automatique, il requiert un nombre limité de personnes et de moyens.
- Un inventaire permanent. Le système de gestion identifie et contrôle à tout moment la situation de la marchandise.
- Une exploitation optimale de l’espace. Les rayonnages optimisent l’espace pour obtenir la plus grande capacité de stockage possible.
Intégration et automatisation
L’automatisation de la logistique permet un flux continu des marchandises, en augmentant la productivité, en minimisant les erreurs et en réduisant les coûts pour Alcorta Forging Group. Son nouvel entrepôt est parfaitement intégré à la production afin de fournir les matières premières nécessaires à la fabrication de près de 20 millions de pièces et composants par an. La technologie est le lien qui relie la production au stockage avec une précision maximale. Les transstockeurs et les convoyeurs accélèrent aussi les processus d’entrée et d’expédition de la marchandise. De plus, le WMS garantit une entière traçabilité des produits.
José Antonio Fernández - Responsable de l’entrepôt d’Alcorta Forging Group à Elgóibar
« L’entrepôt remplit la fonction pour laquelle il a été conçu : s’intégrer parfaitement aux opérations du site de production. Cette solution automatique nous a permis d’optimiser le contrôle des stocks et la préparation des commandes. »
Les avantages pour Alcorta Forging Group
- Une entière traçabilité : grâce à Easy WMS, l’entreprise identifie l’origine et les différentes étapes traversées par chaque produit tout au long du processus de production.
- Un entrepôt intégré : l’entrepôt remplit la fonction importante d’approvisionnement de la production en matières premières et de réception et d’expédition de 150 palettes de produits finis par jour.
- L’optimisation de l’espace : mesurant 13 m de haut et 54 m de long, les rayonnages exploitent l’espace de l’entrepôt au maximum, obtenant ainsi une plus grande capacité de stockage.
Entrepôt d'Alcorta Forging Group | |
---|---|
Capacité de stockage: | 1 115 palettes |
Dimensions des palettes: | 800 / 1 000 x 1 200 mm |
Poids max. des palettes: | 1 300 kg |
Hauteur des rayonnages: | 13 m |
Longueur des rayonnages: | 54 m |
Galerie

L'entrepôt automatisé de pièces détachées automobiles d'Alcorta Forging Group
Demandez conseil à un expert